Crafting Top Quality Water Sports Gear: The Manufacturing Process
Life Jackets and Parasails, from Concept to Reality
Imagine soaring through the air, high above the pristine blue waters, with the wind in your hair and the exhilarating sense of freedom coursing through your veins. Or picture gliding effortlessly across the waves, feeling untouchable and alive. These thrilling moments are made possible by meticulously crafted water sports gear, an intersection of innovative design and rigorous engineering. But have you ever wondered what goes on behind the scenes to create these essential tools for adventure? The journey from a mere sketch to a fully functional parasail or life jacket is a fascinating blend of artistry and precision, brought to life through an intricate manufacturing process: from concept to reality.
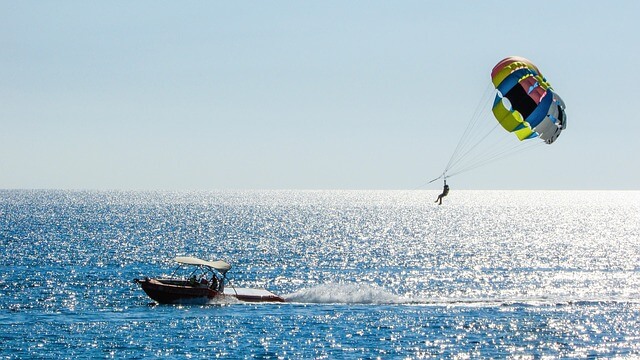
Delving into the heart of this process, we uncover the layers of dedication and expertise required to produce reliable and safe water sports gear. Every parasail and life jacket begins as a concept, a brainchild of designers who blend creativity with functionality. These initial ideas are then transformed through a series of meticulous steps involving material selection, quality control measures, and adherence to stringent safety standards.
Each stage, from the choice of durable fabrics to the final inspection, is crucial in ensuring that every piece of equipment meets industry standards and instills confidence in every thrill-seeker who relies on it. Join us as we explore this captivating journey from concept to reality, uncovering the secrets behind the gear that fuels our aquatic adventures.
Material Selection: Ensuring Durability and Performance
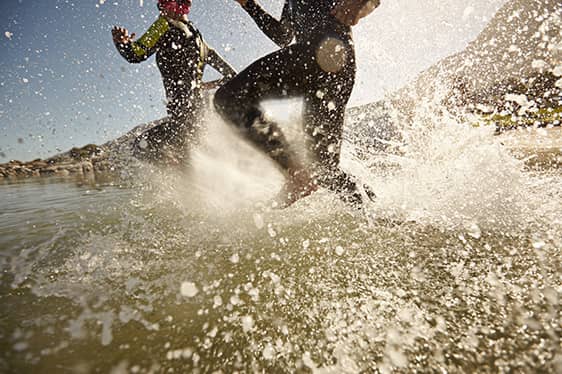
The manufacturing process of water sports gear begins with innovative design concepts. Talented designers with a deep understanding of aesthetics and functionality work tirelessly to create sketches and prototypes that push the boundaries of what is possible. They consider factors such as ergonomics, ease of use, and overall performance to ensure that the final product meets the needs and desires of water sports enthusiasts.
These designers collaborate closely with engineers and experts to transform their ideas into tangible concepts. They refine their designs through brainstorming sessions, computer-aided design (CAD), and physical mock-ups until they are ready for the next stage: material selection.
Prototyping: Bringing Ideas to Life
Once the designs are finalized and materials selected, it’s time to bring these ideas to life through prototyping. Prototypes serve as physical representations of the final product, allowing manufacturers to test functionality, make necessary adjustments, and ensure that all components fit together seamlessly.
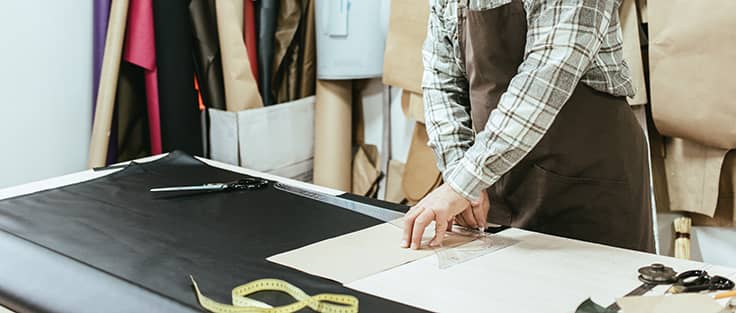
Prototyping involves a combination of manual craftsmanship and advanced manufacturing techniques. Skilled artisans meticulously cut, sew, and assemble the various parts of the gear, paying close attention to every detail. At the same time, computer-controlled machines may be used to create precise components or test specific features.
Throughout the prototyping stage, manufacturers gather feedback from designers, engineers, and even potential users. This iterative process helps refine the design further and ensures any potential issues are addressed before moving on to mass production.
Testing and Quality Control: Meeting Safety Standards
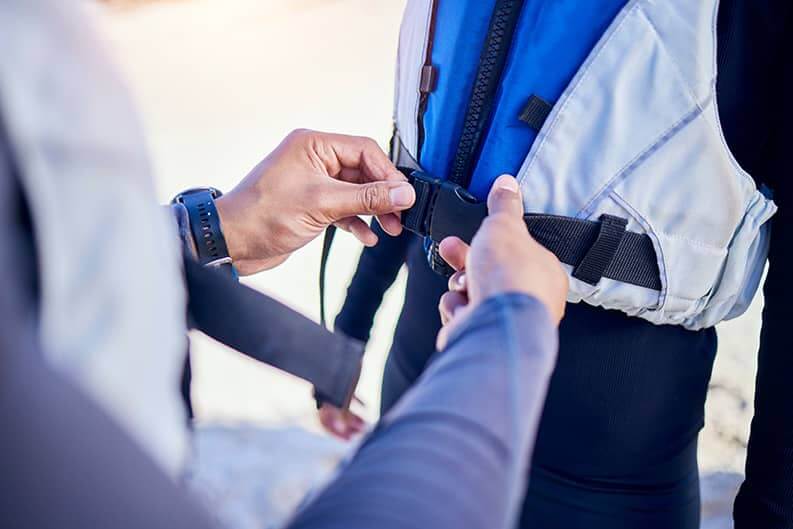
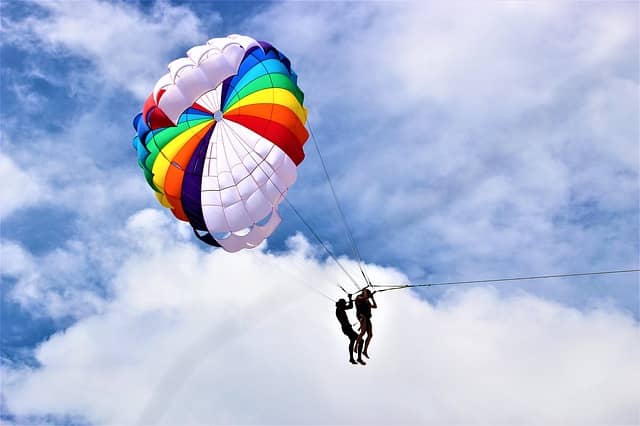
Safety is paramount when it comes to water sports gear. Manufacturers subject their products to rigorous testing procedures to ensure that they meet or exceed industry safety standards.
Parasails undergo extensive wind tunnel testing to assess their aerodynamic performance and stability. Life jackets are tested for buoyancy and proper fit on human models of different sizes. Both types of gear are also subjected to stress tests that simulate real-world conditions, ensuring they can withstand the forces they will encounter during use.
In addition to performance testing, manufacturers implement stringent quality control measures throughout manufacturing. Every component is carefully inspected for defects or inconsistencies before assembly, ensuring that only top-quality materials make it into the final product.
Precision Manufacturing: Crafting with Expertise
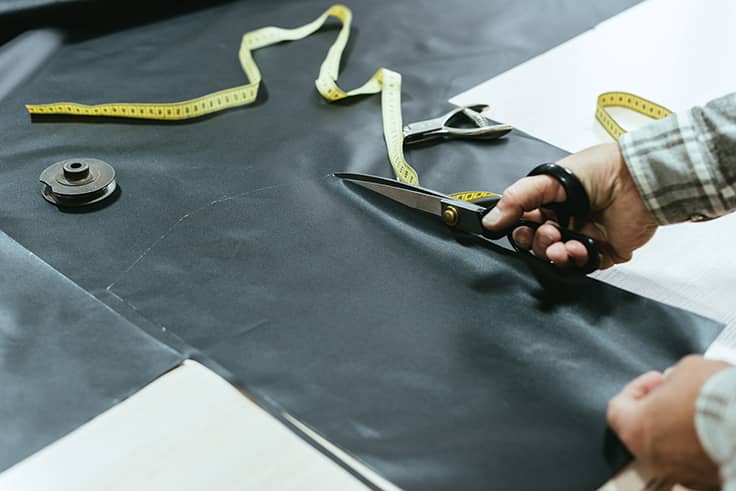
The manufacturing process itself requires a high level of precision and expertise. Skilled technicians operate state-of-the-art machinery to cut fabrics with utmost accuracy, ensuring consistent dimensions across multiple pieces of gear.
Specialized sewing techniques create strong seams that can withstand heavy loads without compromising durability. Welding or bonding methods may be used for components requiring extra reinforcement or waterproofing.
Manufacturers also pay close attention to details like stitching patterns and thread quality. These seemingly small factors can significantly impact the gear’s overall performance and longevity.
Assembly Process: Putting Pieces Together
Once all the individual components have been manufactured, it’s time to assemble them into the final product. Skilled workers carefully follow detailed instructions to ensure each piece is correctly positioned and securely attached.
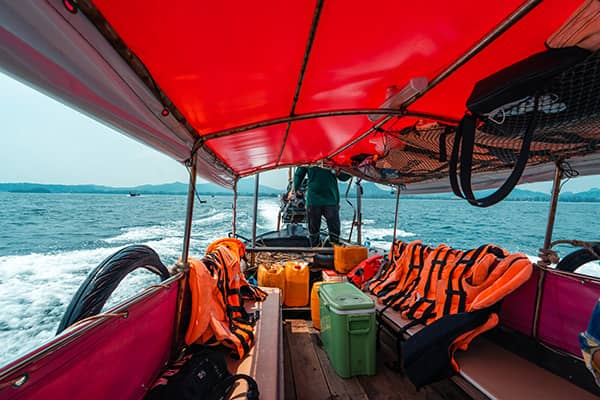
Depending on the complexity of the gear, the assembly process may involve a combination of manual labor and automated machinery. Workers meticulously stitch, glue, or fasten various parts together, paying close attention to alignment and symmetry.
During assembly, manufacturers also add any necessary finishing touches, such as logos, labels, or reflective elements that enhance visibility in low-light conditions.
Compliance with Industry Regulations: Ensuring Safety
Water sports gear manufacturers must adhere to strict industry regulations to guarantee the safety of their products. These regulations cover aspects such as design standards, labeling requirements, and testing protocols.
Manufacturers stay up-to-date with the latest regulations and work closely with regulatory bodies to ensure compliance. They conduct regular audits of their manufacturing processes and facilities to maintain high standards of safety and quality.
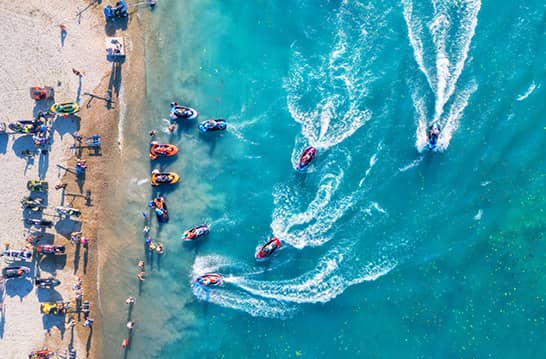
Final Inspection: Guaranteeing Reliability
Every piece of water sports gear undergoes a thorough final inspection before packaging and shipping. This step is crucial in identifying any potential defects or issues that may have been missed during earlier stages of production.
Dedicated quality control teams meticulously examine each item for proper construction, functionality, and overall appearance. Any deviations from the desired specifications are immediately addressed before the gear is deemed ready for market.
Packaging and Shipping: Preparation for the World
The last stage in the manufacturing process involves carefully packaging each piece of water sports gear for shipment. Manufacturers use appropriate packaging materials and techniques to protect the gear from damage during transit.
Each item includes labels and instructions that provide users with important information on proper usage, maintenance, and safety precautions. Manufacturers also ensure their packaging is environmentally friendly, opting for recyclable materials whenever possible.
Once packaged, the gear is ready to be delivered to water sports enthusiasts around the world. From concept to reality, each piece represents the culmination of countless hours of design, engineering, and manufacturing expertise.
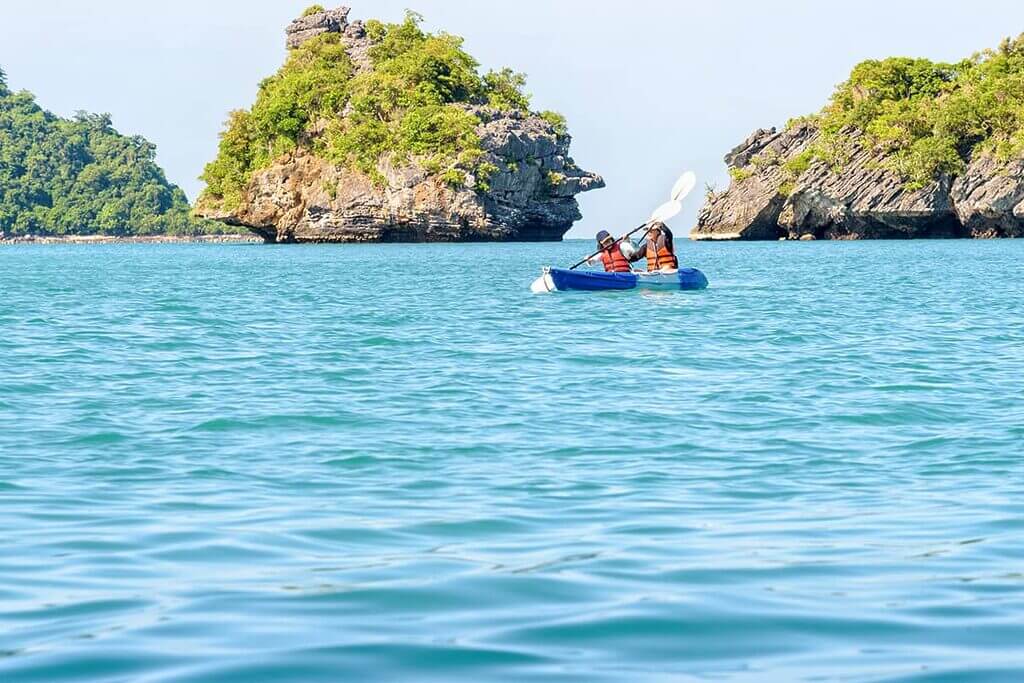
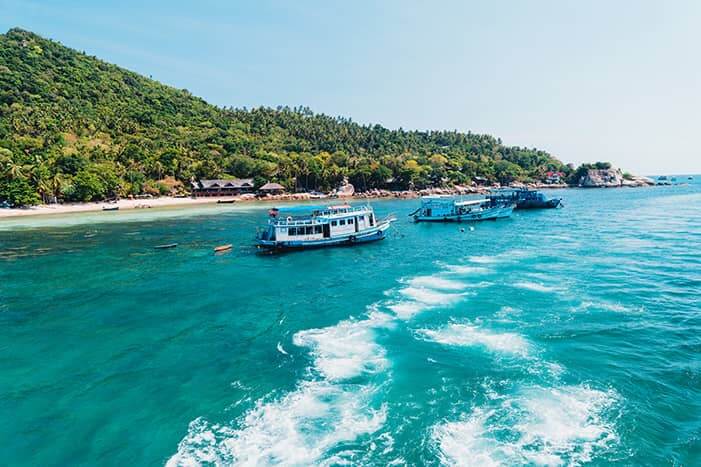
The Art and Science Behind Water Sports Gear
The manufacturing process of water sports gear is a captivating blend of artistry and precision. From innovative design concepts to meticulous material selection, prototyping, testing, and assembly, every step plays a crucial role in creating reliable and safe equipment.
Manufacturers prioritize durability, performance, and adherence to industry regulations throughout the entire process. They combine state-of-the-art machinery with skilled craftsmanship to bring ideas to life while ensuring that each piece meets or exceeds the highest quality standards.
The next time you strap on a parasail or don a life jacket before embarking on your aquatic adventure, take a moment to appreciate the intricate journey that brought that gear into existence. It’s a testament to the dedication and expertise of those who craft these vital tools for our enjoyment and safety.